8 Ways to Increase Employee Efficiency
In today’s fast-paced business environment, there are various steps on how to improve employee efficiency, from streamlining from streamlining business process operations management to providing the right tools and training.
In this blog, we'll delve into eight practical strategies for boosting how to improve employee efficiency through a refined approach to business process operations management within your organization. We'll examine how each process can be elevated through targeted training and development, effective organizational strategies, and the utilization of the right products from IRSG. By adopting this comprehensive strategy, businesses can experience significant improvements in employee productivity, heightened customer satisfaction, and ultimately, a stronger bottom line. Embracing these practices will position your business for success in an ever-evolving and competitive retail landscape.
Mastering Shipment Efficiency
The efficiency of a business is largely dependent on the efficiency of its employees. And when it comes to managing shipments, optimizing the process can make a huge difference in productivity and profitability. Monitoring this process using the right resources, standard operating procedures, and effective time tracking will boost accountability and reduce time spent accomplishing these tasks. Here are a few tips for improving the shipment process within your organization:
- Implement a Standard Operating Procedure (SOP): This includes developing clear and concise steps for managing the shipment process. Ensure employees understand and are trained on these procedures to promote consistency throughout the process.
- Utilize the Right Resources and Streamline Receiving and Processing: Equip employees with the appropriate tools to streamline the shipment process. IRSG’s innovative racks and carts are designed to optimize efficiency in this process. Use carts and rolling racks to unload, fold, or hang merchandise by size, color and department. This makes it easier to transport the items to their delegated areas and ensures smooth inventory management.
- Monitor Time and Accountability: Track time spent during the shipment process to identify areas that can be improved. Consider using time tracking tools or implementing time limits for specific departments or tasks.
- Continuously Improve: Regularly assess and review your shipment processes to identify areas for improvement. Encourage employee feedback and suggestions to gather valuable insights on enhancing efficiency further.
By utilizing this strategy, businesses can improve their shipment best practices from receiving goods, to processing goods, to transporting them to the sales floor. The streamlined process will lead to reduced processing time and increased productivity. These tips will improve profitability, positioning your business for success in a competitive market.
Improving Your Markdown and Signage Process
Improving employee productivity in the signage and markdown process is crucial for profitability and overall customer experience within retail environments. By ensuring products are appropriately marked down and signed, employees can more efficiently move merchandise and ensure a consistent customer experience. To increase employee efficiency in the markdown and signage process we suggest utilizing these tips:
- Develop Clear Guidelines: Establish clear guidelines and procedures for markdown and signage. Provide employees with specific instructions on how to mark down products accurately and effectively. Consistent signage placement and scanning from left to right for efficient workflow.
- Utilize IRSG's Marketing Carts: IRSG's marketing carts are designed to keep all the necessary materials organized and easily accessible. Equip employees with carts to ensure they have quick access to signage, pricing labels and scanning devices for the markdown and signage process. This eliminates time wasted searching for supplies, enabling employees to focus on their tasks.
- Optimize Product Movement: Train employees on the proper techniques for moving products during the markdown and signage process. Encourage them to efficiently move products as needed to ensure accurate signage placement. Starting at walls and progressing to tables helps maintain consistency and streamline the process. Emphasize the importance of maintaining an organized workspace to minimize distractions and improve efficiency.
- Foster Collaboration: Encourage collaboration and teamwork among employees involved in the markdown and signage process. By working together, they can divide tasks, streamline workflows, and support each other when needed.
By following these steps, employees will be able to work more effectively, ensuring accurate and consistent signage while maximizing their productivity. This ultimately leads to improved customer experiences and increased profitability for the business.
The Key to Effective Visual Merchandising
Visual merchandising is an essential component of any successful retail business. By creating enticing displays and following company guidelines for floor sets, businesses can attract customers and boost sales. To do this, it's important to have a well-organized and efficient system for setting up displays and changing floor sets. To increase employee efficiency in the visual merchandising process, follow these steps:
- Plan Ahead: Develop a clear plan and guidelines for visual merchandising, including floor sets and display changes.
- Utilize IRSG's Transporters, Rolling Racks, and Visual Carts: IRSG's innovative tools, such as transporters, rolling racks, and visual carts, are specifically designed to streamline the visual merchandising process. These resources enable employees to efficiently transport and organize display items, saving time and effort.
Organize Display Items: Train employees on effective organization techniques for display items. Teach them to arrange products by category, theme, or season, ensuring visual coherence and ease of customer navigation. By organizing display items in advance, employees can quickly and easily set up new displays, minimizing downtime.
- Implement Time-Saving Techniques: Encourage employees to use time-saving techniques during the visual merchandising process. This may include utilizing hanging systems or grids for quick display changes, and optimizing the layout of rolling racks and visual carts to streamline access to materials.
By utilizing these resources, businesses can quickly and easily set up new displays and floor sets, reducing the time it takes to complete the task and freeing up employees to focus on other areas of the business.
Fitting Room and Sales Floor Organization
Effective organization is essential to increasing employee efficiency in retail environments. This is particularly true when it comes to fitting room and sales floor organization. By ensuring that products are properly processed and returned to the sales floor, businesses can reduce clutter and confusion, making it easier for employees to find what they need and help customers. To increase employee efficiency in fitting room and sales floor organization, follow these steps:
- Establish Clear Processes: Develop a SOP for processing products back to the sales floor. Ensure employees understand the steps involved and the expected outcomes. Provide training and ongoing guidance to reinforce these processes.
- Utilize IRSG's Racks, Carts, and Transporters: These racks, carts, and transporters are designed to optimize efficiency in the organization and transportation of items. Use racks and carts to sort and store returned items, and utilize transporters for easy and swift movement of products back to the sales floor.
- Implement Hanger Management Systems: These systems facilitate the sorting and organization of hangers, making it easier for employees to quickly retrieve and return them to the appropriate areas. Organized hanger management saves time, reduces labor costs, and clutter.
- Designate Specific Areas: Create designated areas in your store for processing and organizing items from fitting rooms or returns. Have separate sections on racks or carts for different departments or categories to ensure efficient sorting. This allows employees to quickly identify and place items in their appropriate locations, minimizing confusion and enabling faster restocking.
- Optimize Product Placement: Arrange products on the sales floor in a logical and visually appealing manner. Implement a systematic approach to product placement, considering factors like size, color, and seasonality. Train employees on effective merchandise presentation techniques, such as front-facing and consistent sizing, to enhance the customer shopping experience and expedite product retrieval.
By utilizing these steps, employees will have the tools and resources needed to process items efficiently, return them to the sales floor promptly, and create a well-organized shopping environment for customers. This not only enhances productivity but also improves the overall shopping experience and contributes to the success of the business.
Efficient Inventory and Stock Management Processes
Inventory and stock management is a critical component of any successful retail business. By keeping track of inventory levels, reorganizing and replenishing products as needed, businesses can ensure that they always have the right products in stock and can minimize waste. However, inventory and stock management can be time-consuming and labor-intensive, especially for larger businesses. Follow these steps to increase employee efficiency in your inventory and stock management process:
Implement Inventory Management Systems: Invest in a reliable inventory management system that provides real-time visibility of stock levels, tracks product movement, and generates accurate reports. Train employees on how to use the system effectively, including updating inventory records, conducting stock counts, and generating replenishment orders regularly.
- Enhance Organization: Clearly label and arrange storage areas, such as shelves or designated sections to easily locate and access items. By utilizing IRSG's inventory storage solutions such as replenishment racks and merchandise carts to optimize space utilization and accessibility. Arrange products systematically based on factors like category, size, and popularity, making it easier for employees to locate and restock items efficiently. Identify high-demand items and position them strategically to enhance visibility and accessibility.
- Set Replenishment Thresholds: Establish clear guidelines for replenishing stock levels. Determine minimum and maximum inventory thresholds for each product and category, triggering reorder points when stock reaches predetermined levels. By having automated replenishment systems in place, employees can focus on managing exceptions and addressing urgent inventory needs.
With these methods and resources, employees can work more efficiently, spending less time restocking inventory or searching for products and more time helping customers and generating sales.
Return Management Best Practices
Efficient returns management is essential for any business, as it not only impacts customer satisfaction but also affects employee productivity. Handling returns can be a complex process, requiring careful organization and coordination to ensure items are processed promptly and accurately. Increase employee efficiency within your organization with these steps:
- Establish Clear Return Policies: Develop clear and concise return policies that are easily accessible to both customers and employees. Ensure that employees are trained on these policies, including eligibility criteria, timeframes, and procedures for processing returns. Clear guidelines help employees handle returns more efficiently and provide consistent service to customers.
- Streamline Sorting and Categorization: Utilize IRSG's transporters and carts to organize and sort returned items efficiently. Designate specific areas for different types of returns, such as defective items, customer exchanges, or restockable merchandise. Train employees on how to quickly assess returned items, determine their appropriate category, and sort them accordingly. Efficient sorting minimizes processing time and reduces errors.
By following these steps and leveraging IRSG's processing and transport solutions, businesses can streamline their returns process, overall increasing employee efficiency. Employees will be equipped with the tools and strategies necessary to handle returns promptly and accurately, minimizing disruptions and maximizing productivity.
Minimizing Loss of Damaged Products
Efficient handling of damaged goods is crucial for businesses to minimize losses and maintain customer satisfaction. Dealing with damages requires a well-organized and streamlined process, which can significantly impact employee efficiency. Here are our suggestions to implement in your business:
- Establish Clear Guidelines: Develop clear guidelines and procedures for handling damaged products. Train employees on how to identify damaged items, including specific criteria and indicators. Provide clear instructions on how to document and report damaged products accurately. Clear guidelines ensure that employees can quickly assess and categorize damaged items without confusion.
- Utilize IRSG's Organizational Solutions: Implement IRSG's tables, bins, carts, and wire racks in dedicated processing areas for damaged products. Utilize tables for efficient sorting and inspection of damaged items. Use bins or designated storage areas to separate and store damaged goods awaiting further action. Deploy carts and wire racks for easy transportation and organization of damaged products.
- Expedite Return to Warehouse: Establish an efficient process for returning damaged items to the warehouse or designated storage area. Utilize IRSG's carts or mobile packing station to facilitate the movement of damaged products. Designate specific pick-up points or scheduled collection times to optimize the return process. Promptly returning damaged items to the warehouse minimizes the risk of further damage and loss.
Streamlining your Ship from Store Process
Ship From Store, (SFS) and online ordering have become integral parts of the retail landscape, requiring businesses to optimize their processes to meet customer demands efficiently. The key to increasing employee efficiency in these areas lies in utilizing the right tools and systems. To increase your employee productivity and efficiency around online ordering and SFS process. Here are our tips:
- Implement Standard Operating Procedures (SOPs): Develop clear SOPs for the ship from store process. Outline step-by-step instructions for receiving, picking, packing, and shipping orders. Train employees on these procedures to ensure consistency and efficiency. SOPs eliminate guesswork and confusion, allowing employees to complete their tasks more effectively.
- Utilize IRSG's Omni and E-commerce Solutions: Implement IRSG's picking carts, mobile packing stations and security cages that are designed specifically for ship from store processes. Picking carts provide a mobile and organized solution for collecting items from the sales floor or back of house. Security cages ensure the secure storage of high-value or sensitive items during the picking process. Packing stations offer a centralized and efficient area for packaging orders. Leveraging these innovative tools improves organization and accessibility, enabling employees to process orders more quickly.
Train Employees on Efficient Order Fulfillment: Provide comprehensive training to employees on efficient order fulfillment techniques. Train them on proper order picking methods, effective packaging practices, and utilizing the available tools and systems. Emphasize the importance of accuracy and speed while maintaining quality standards. Regularly review and provide feedback to further enhance employee efficiency.
Businesses can enhance the efficiency of their ship from store and online order fulfillment operations, ultimately leading to faster turnaround times, improved accuracy, and heightened customer satisfaction with these solutions.
Employee Efficiency in your Business
In conclusion, prioritizing employee efficiency is paramount for businesses striving to thrive in today's competitive and fast-paced marketplace. Increasing employee efficiency is an ongoing journey. Regularly evaluating performance, gathering feedback from employees, and identifying areas for improvement are vital steps towards achieving optimal efficiency. By adopting a proactive and solution-oriented approach, businesses can continuously enhance their operations and maintain a competitive edge in the dynamic retail landscape.
In summary, by prioritizing employee efficiency through training, organization, and the strategic utilization of IRSG's innovative products, businesses can unlock their full potential and elevate their performance across various operational processes. Embracing efficiency not only benefits the bottom line, but also contributes to a positive work environment and enhances the overall customer experience.
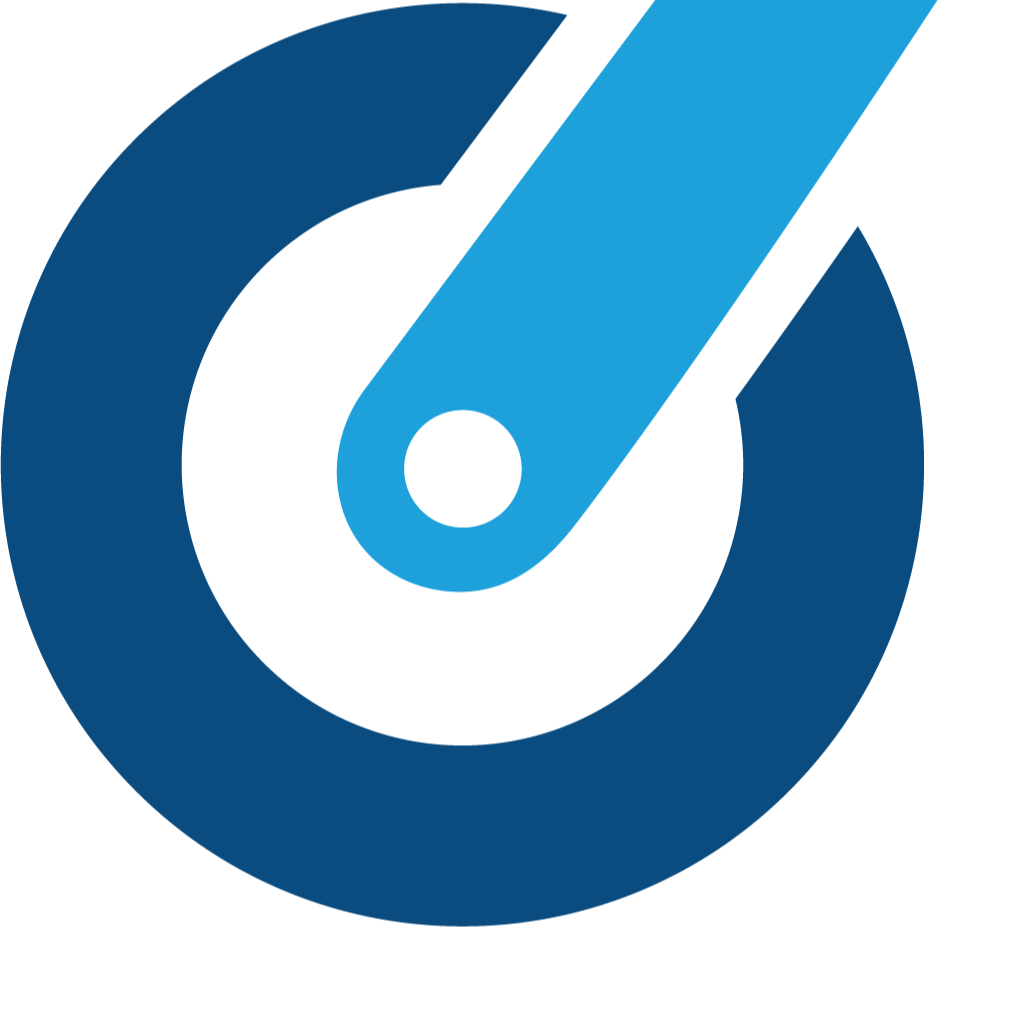
IRSG
IRSG has been providing the industry’s highest quality, longest lasting, and most versatile Inventory Processing and Transport Systems since 1968. We are the market leader. We design solutions where others hadn’t recognized the need for improvement, and our vision has prompted us to create over 200 unique, flexible, and durable solutions for a vast array of retail needs. IRSG offers a wide range of products, allowing you to find everything you need, all from one supplier. Each and every solution has one goal: to successfully streamline your business from the back door to the sales floor in an efficient, organized approach.